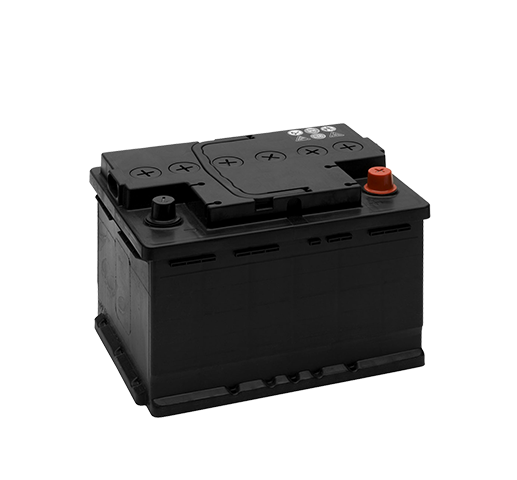
We will be covering fuel injection: design, function, inputs and outputs, diagnosis and testing.
Overview
In the past distributors, controlled spark timing and carburettors controlled the fuel going into an engine. Nowadays these functions are computer controlled and the results are increased power, economy, response and reduced emissions. The system is referred to as fuel injection or engine management.
Inputs
Different fuel ratios are needed for different conditions and loads. For example, a rich mixture (eg 12:1) gives more power and is used under load such as accelerating, while a lean mixture (eg 17:1) is used when cruising and is more economical.
The optimum air/fuel ratio for complete combustion and minimal emissions is 14.7:1, and is termed the stoichiometric ratio.
The ECU (electronic control unit) or management computer needs to know what is happening, is the vehicle travelling at full throttle up a long hill at 3000rpm in very hot conditions? Or is the engine cold and idling after startup for the first time that day? For the ECU to control combustion and make sure that the air and fuel are mixed in the right proportions under all conditions, and that each cylinder’s spark plug is fired at the right time, the ECU needs to know precisely what is going on.
It does this through the input sensors such as:
- Coolant temperature sensor
- Airflow meter
- Manifold absolute pressure sensor (MAP sensor)
- Crankshaft position sensor
- Camshaft position sensor
- Exhaust gas oxygen sensor
- Throttle position sensor
- Road speed or vehicle speed sensor
- Atmospheric pressure sensor
- Knock or detonation sensor
I am not going to explain how each sensor works in this column, all you need to know is that all are needed to tell the ECU about various engine parameters to control the spark timing and fuel injection ratios precisely under all possible conditions.
Outputs
Once all the inputs have been taken into account the ECU sends electrical signals to the outputs such as:
- Fuel injectors
- Ignition coils or modules
- Idle up or idle control valves
- Exhaust gas recirculation valve (EGR)
- Variable camshaft timing valves (if equipped)
In addition to the above functions, most ECU’s are able to ‘learn’ about the engine’s state of tune. For example, imagine if your fuel filter is partially blocked, causing the mixtures to always be a little lean.
The exhaust gas oxygen sensor reads this and in response, the ECU enriches the air/fuel ratio, instead of doing this every time the injectors are fired, the ECU will adjust the ratio permanently. If you change the filter and more fuel gets through, the mixture will now be rich for a while until the computer learns that new requirements are needed.
One of the most useful functions that modern ECU’s have is the self-test function. If there is a fault with the system, by connecting a diagnostic scan tool or bridging wires together a technician is able to receive a code from the ECU and be directed to the area where the fault is.
Further diagnosis is usually needed but at least the technician knows which area to look in and which components to test. Thanks for reading, if you have any questions or comments please get in touch.